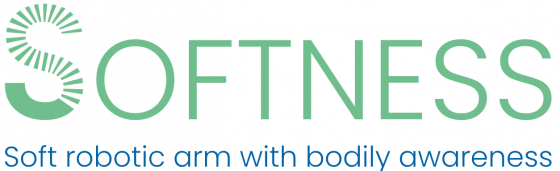
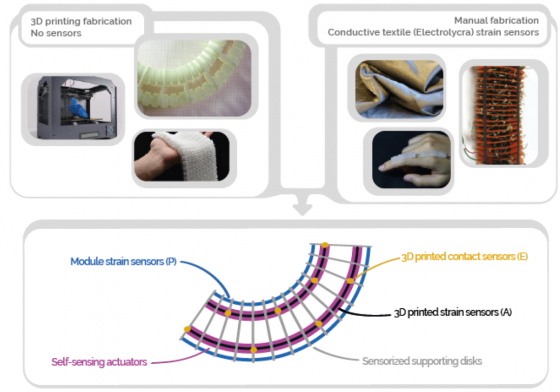
Proprioception is the sense that lets us perceive the location, movement, and action of parts of the body. Thanks to proprioception, for example, we can drink a glass of water with closed eyes. Any stimulus coming from outside the body is sensed owing to exteroception, including, among others, touch and pressure. Human beings can take these senses for granted, but this is not the case for robots, especially if they are "soft” to ensure safe human-robot interaction.
Research on soft robotics is becoming increasingly important worldwide, but how soft robots can sense their bodies and interact with the external environment remains an open question and a challenge, due to their continuously deformable structure, which imposes the use of flexible and light sensors.
Stretchable strain sensors based on smart textiles or electrically conductive polymers are good candidates, being non-invasive, flexible, easy to use, and inexpensive. Common devices are piezoresistive strain sensors, whose electrical resistance changes in response to an applied mechanical stretching. The main drawbacks of these soft materials are their remarkable electromechanical hysteresis and nonlinear relaxation dynamics, which must be accurately compensated to properly exploit them as sensors.
Additionally, in general, soft robots are still produced with high manual effort: the higher the complexity of the robot, the higher the skill needed by human operators, together with the increase in time and costs for fabricating and assembling. As a consequence, a further research challenge is the automatization and production standardization of these robots. In this context, 3D printing is very promising, having the potential of fabricating soft structures with embedded actuators and sensors. This will pave the way for fully automated manufacturing of sensorized and custom-made soft robots.
SOFTNESS aims to design a 3D-printed, sensorized soft robotic arm, able to sense its spatial configuration (proprioception) and detect contact with external objects (exteroception). Both already available stretchable sensors (e.g., made of conductive textiles) and custom 3D-printed sensors, made of conductive composite materials based on a polymeric matrix, will be used. Model-based and data-driven approaches will be used to compensate for the intrinsic nonlinearity of these sensing materials, allowing for proper exploitation as strain and contact sensors. Signals provided by several sensors installed on the arm will be elaborated through an embedded device, to reconstruct the spatial configuration of the arm and the contact location of external stimuli, in real-time. SOFTNESS will then provide a custom 3D-printed soft robotic arm with proprioception and exteroception capabilities that will enable its accurate control, which is now possible only by resorting to invasive and bulky external optical sensors that can limit the movements of the arm.